Amazon Robotics has come a long way since its inception over a decade ago, following Amazon’s acquisition of Kiva Systems in 2012. Now, with over 750,000 robots deployed across its operations network, Amazon is revolutionizing its fulfillment processes.
The goal of this advanced robotics technology is straightforward: to pair employees with the right machines, making their workday safer, easier, and more productive, while simultaneously ensuring faster deliveries for customers. The most recent example of this is the new state-of-the-art fulfillment center in Shreveport, Louisiana. This facility is equipped with Amazon’s latest robotics innovations, supporting employees who package and ship customer orders.
This center uses eight different robotic systems that work in concert to fulfill and deliver packages. These systems are designed to contribute to safety enhancements, productivity gains, and career benefits, according to a recent MIT study.
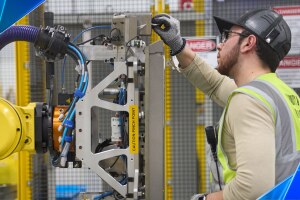
Cloud computing infrastructure, provided by Amazon Web Services, ensures that these robots operate efficiently. They store and process the vast amount of data generated by sensors, cameras, and machine processes. Amazon plans to gradually integrate these sophisticated robotics systems into other existing facilities throughout its network.
“Years of innovation have allowed us to build, test, and scale this unique, highly integrated suite of robotics systems that support our employees in fulfilling customer orders,” said Scott Dresser, vice president of Amazon Robotics. “Thanks to advances in AI, these technologies integrate seamlessly, and will help us drive an estimated 25% productivity improvement at next-generation fulfillment facilities. This allows us to deliver more efficiently for customers, while supporting the employees who make it happen.”
Let’s follow the journey of a package, guided by the eight different robots supporting next-generation package fulfillment at Amazon.
1. Sequoia
Before the fulfillment process begins, Amazon’s sophisticated inventory planning system determines the correct storage of products in fulfillment centers near customers. The Sequoia robotic system, utilizing AI, robotics, and computer vision, consolidates inventory and frees up storage space at the site. This results in faster order processing.
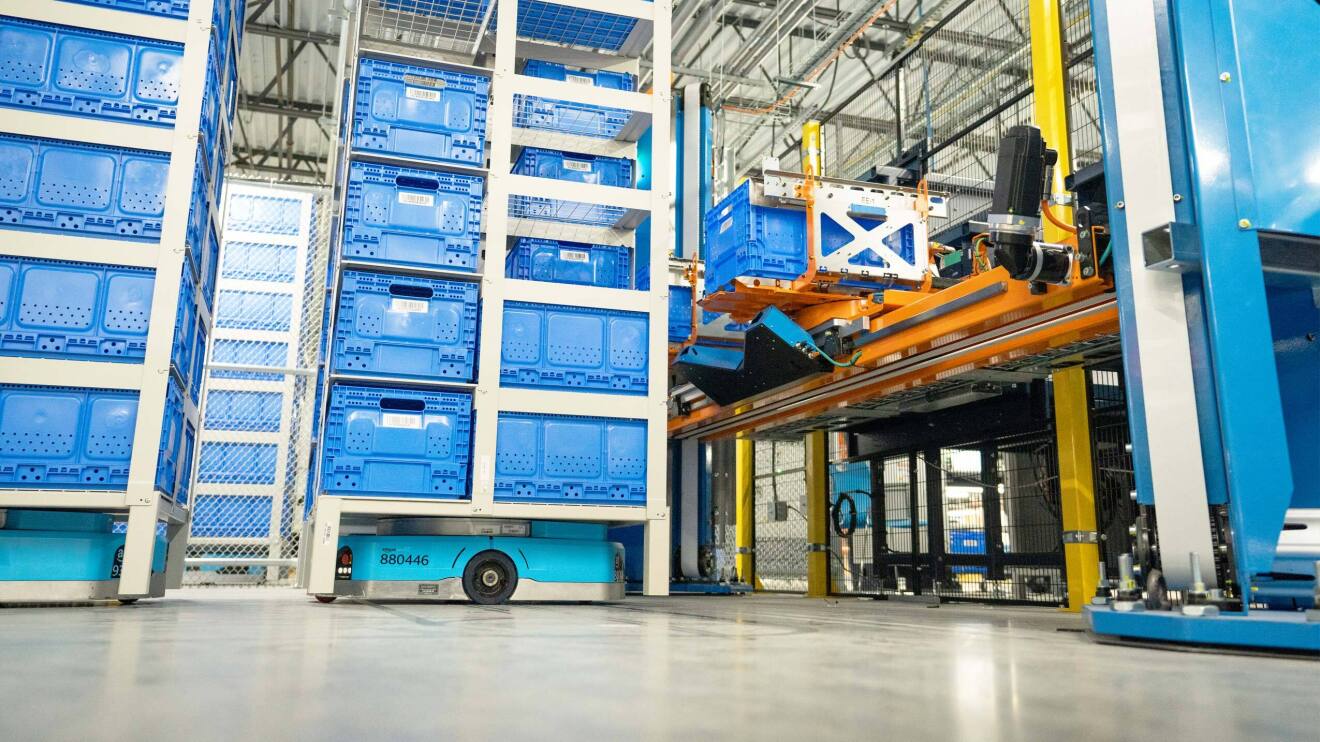
Sequoia can identify and store inventory up to 75% faster in Amazon fulfillment centers. Mobile robots transport inventory directly to a containerized storage system, or to an employee who is picking items for a customer order. Inventory is brought directly to employees at a workstation specially designed for their power zone (between mid-thigh and mid-chest), reducing the need for employees to reach above their heads or squat down. These designs help to mitigate common workplace injuries.
2. Hercules
Employees utilize several robotics systems to select items for customer orders. Hercules is a drive unit that finds and transports pods of items from various parts of the fulfillment center to employees who pick items before packaging.
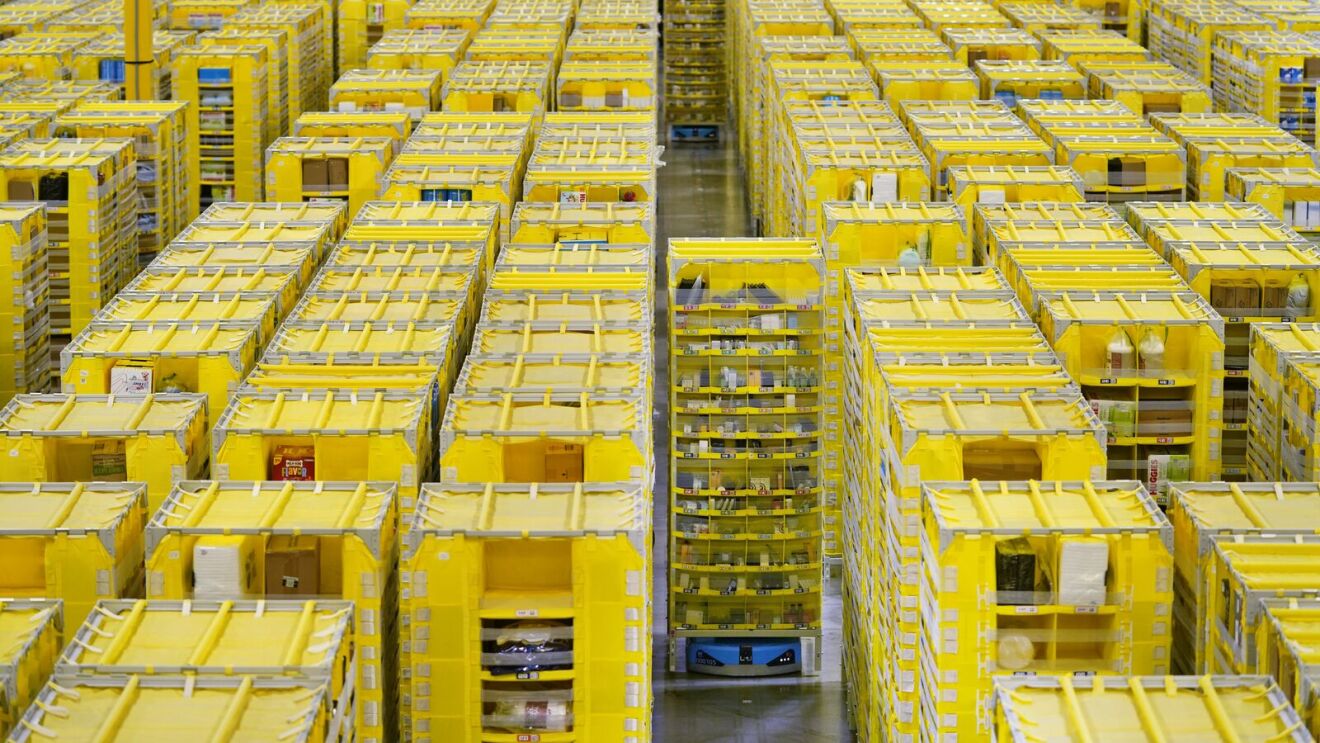
Hercules makes independent movement decisions based on centralized planning software. It uses a forward-facing 3D camera to differentiate people, pods, and other objects. This technology enhances safety by allowing Hercules to make informed choices about its path. To navigate, find its location, and locate any pod, Hercules uses its camera to read a grid of encoded markers on the floor.
3. Titan
Similar to Hercules, Titan is another drive unit designed to transport items from across Amazon’s fulfillment centers straight to employees. What makes Titan unique is its lifting capacity, which is twice that of Hercules. As a result, Titan handles larger or bulkier items, such as small household appliances or pallets of food.
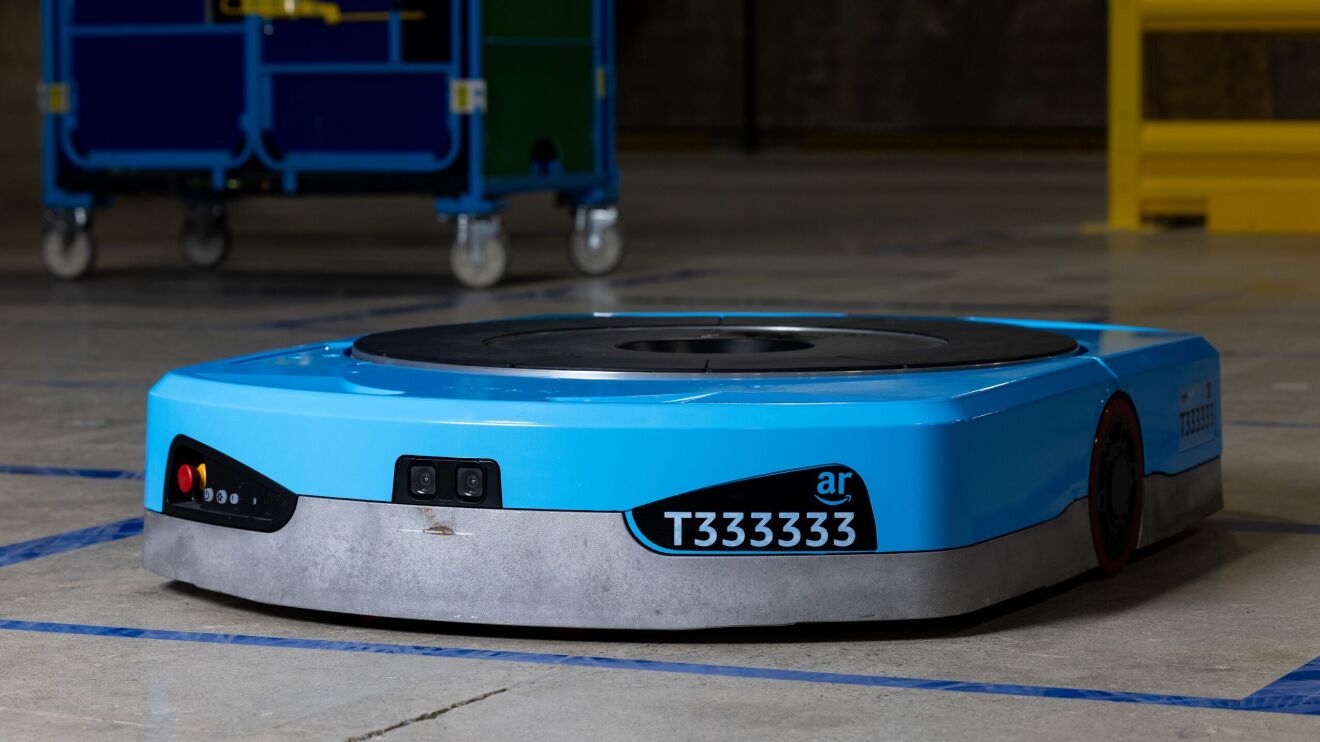
Titan picks up pods of totes and navigates through a restricted robotics floor using computer vision.
4. Sparrow
Supporting employee efforts to combine items for customer orders, Sparrow is another robotic system. The robotic arm picks up and moves individual items from containers into designated totes, sending them to employees before packaging.
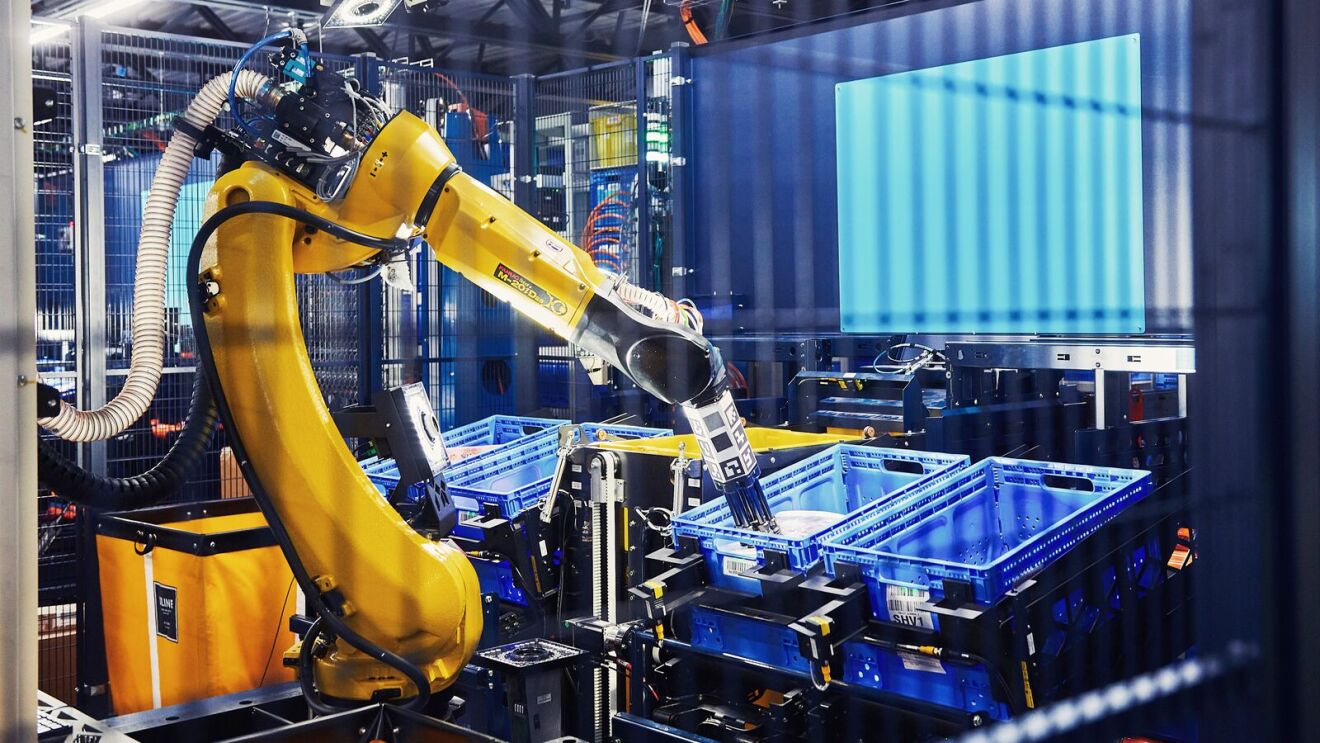
Sparrow uses computer vision and AI to identify the correct item and place it in the tote as it moves toward the employee.
5. Packaging Automation
Following the selection of all the items for a customer order, Amazon uses various packaging innovation systems to package orders with sustainability in mind.
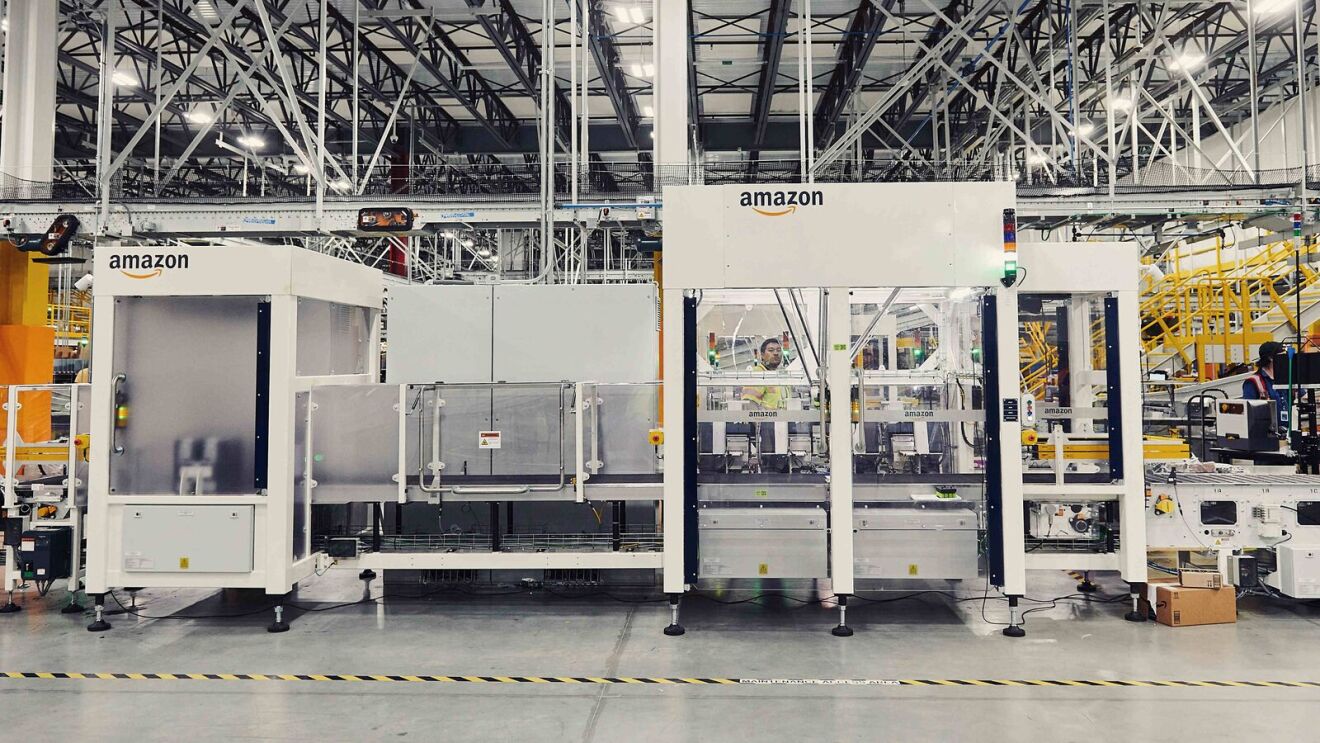
These machines were originally designed to create plastic bags, but have been retrofitted to create made-to-fit paper bags. Sensors are used to measure an order’s dimensions. The device then creates a custom-sized protective bag using durable, weather-resistant paper and heat-sealing technology.
By allowing the use of curbside recyclable materials, more customers can recycle at home. Across the U.S., more than 120 of these machines have been retrofitted in over 20 fulfillment centers, which helps to avoid the use of more than 130 million plastic bags this year.
6. Robin
Once a package is boxed, it starts its journey to the outbound dock, where it will be loaded onto a truck. Robin was Amazon Robotics’ first deployed robotic arm and was designed to sort packages before they are brought to the outbound dock.
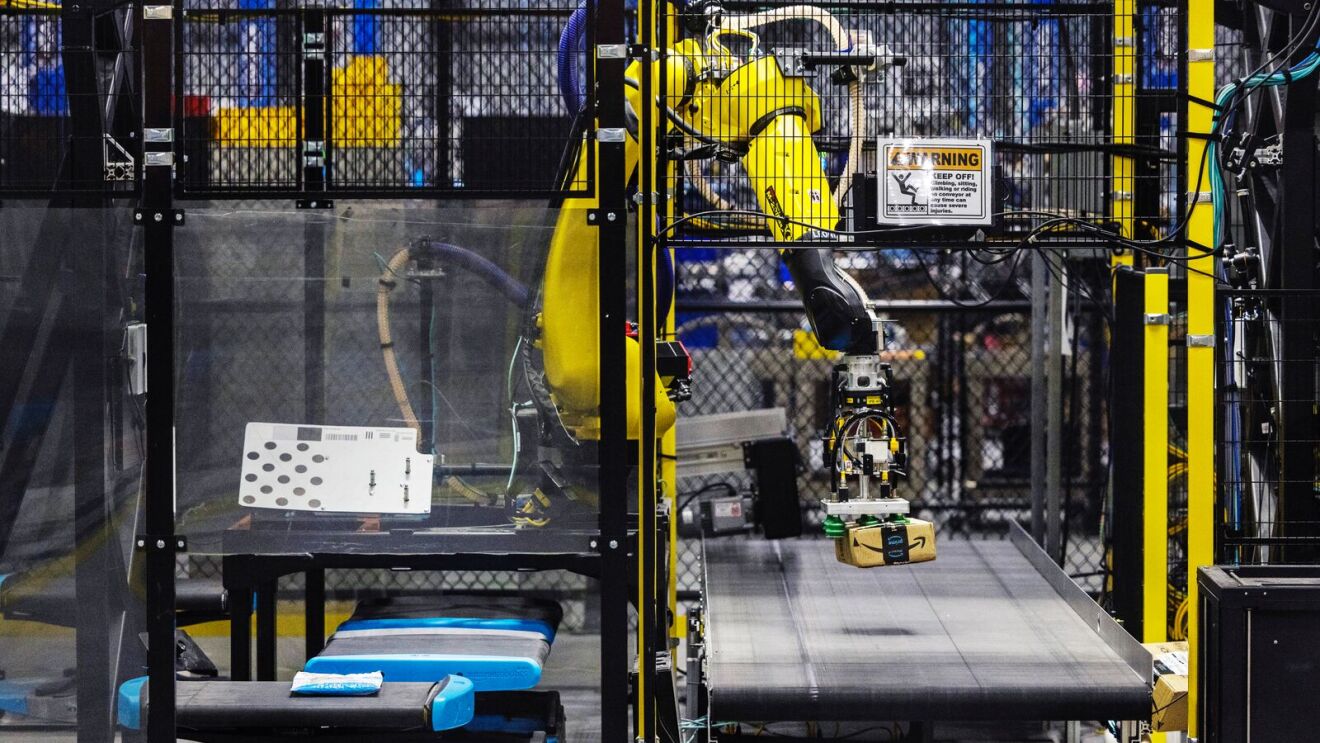
Robin grabs packages off of conveyor belts and places them onto robotic drive units for onward transport within the facility. It also transfers damaged packages to ensure optimal quality control.
7. Cardinal
Similar to Robin, Cardinal is a robotic arm that uses advanced AI and computer vision to rapidly select a package out of a group of packages. The robot then lifts the package using air suction, reads the label, and precisely places it in the appropriate cart, making it ready for transport to a truck. This helps reduce the risk of injury for employees handling larger packages, since Cardinal can handle packages weighing up to 50 pounds.

8. Proteus
Proteus is Amazon’s inaugural fully autonomous mobile robot. It has the capability to navigate freely throughout a site, using sensors to detect and avoid any objects in its path. Unlike other mobile robots like Titan and Hercules, which operate in restricted areas, Proteus can move seamlessly throughout the fulfillment center environment.
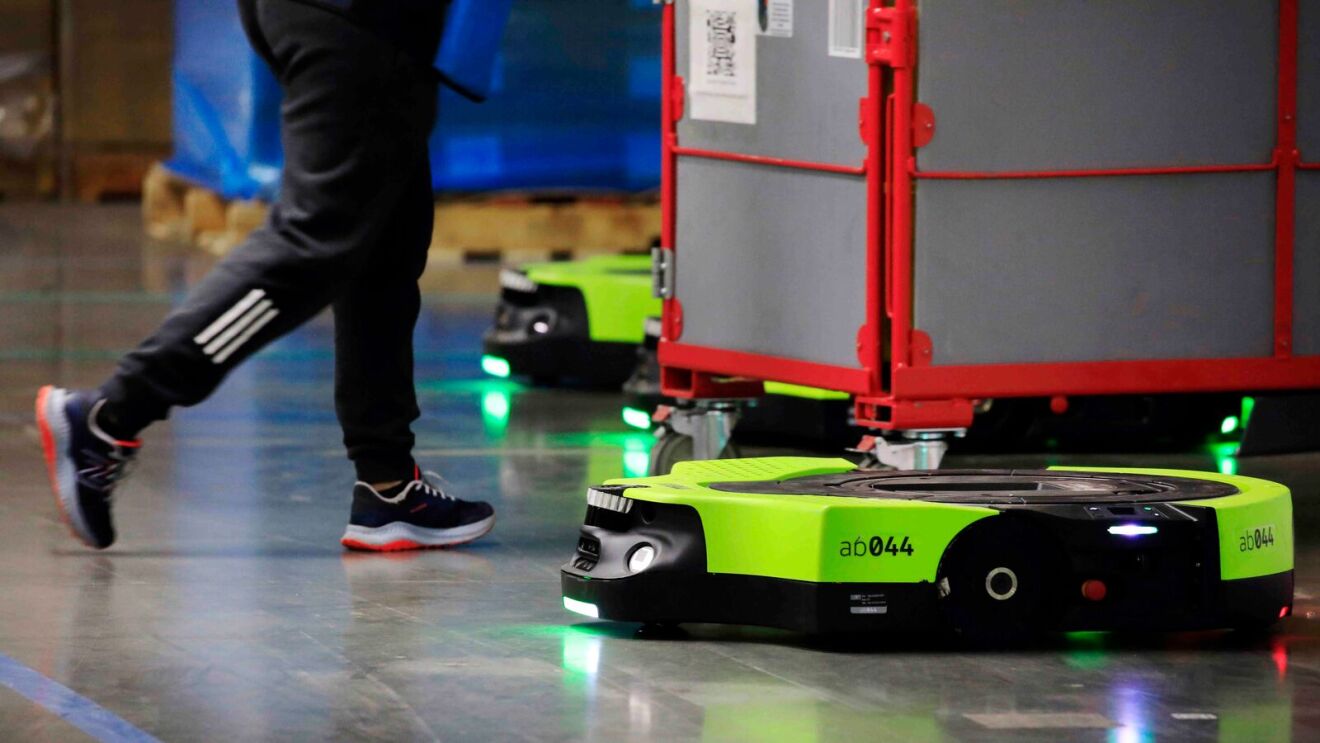
Proteus collaborates with Cardinal, a robot arm that loads packages into carts. Together, they move carts from the fulfillment center’s outbound dock to the loading dock where packages are loaded onto delivery trucks.