When Amazon started selling books in 1995, the company operated from a humble garage. Today, our global fulfillment network is powered by advanced technology and artificial intelligence.
Over the years, the company has developed and scaled the world’s largest fleet of industrial robots to ease tasks for employees, improve operational safety, and create hundreds of thousands of new jobs. Amazon has over 750,000 robots that sort, lift, and carry packages.
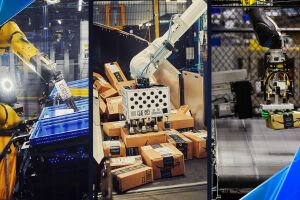
Amazon has deployed eight different robot models across its operations to provide employees with the right technology to make their workday safer.
The company is entering a new era with the introduction of its most significant advancement in robotics and AI technologies in the company’s history. Located in Shreveport, Louisiana, the next-generation fulfillment center combines years of innovation under one roof, transforming how Amazon works and setting a new standard for industry efficiencies.
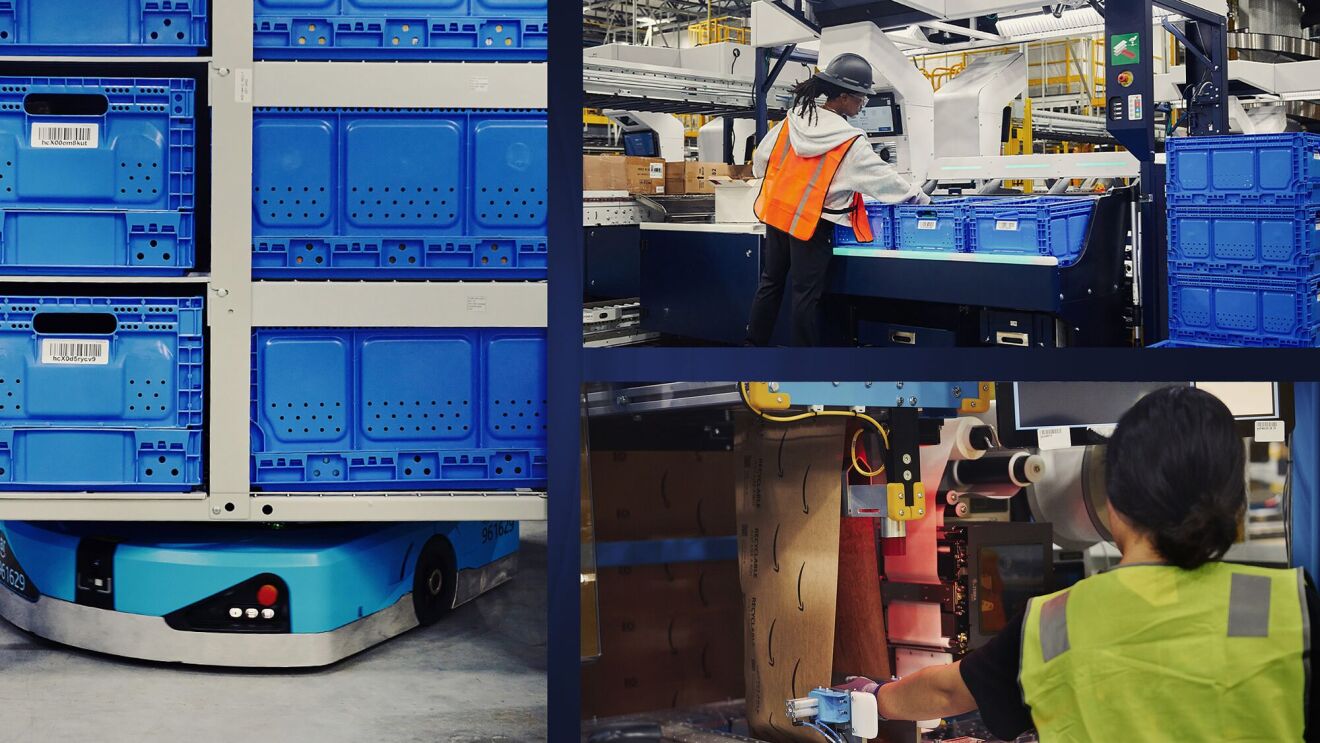
The facility spans five floors and more than 3 million square feet—equivalent to 55 football fields—making it one of Amazon’s largest sites. The center will employ 2,500 employees once fully operational.
Amazon provides competitive pay, training and upskilling opportunities, and a comprehensive benefits package for fulfillment center employees. This makes the company a great place to begin or advance a career.
For the first time, Amazon has introduced technology solutions in every key production area at the Shreveport site. As a result, employees will work alongside a growing fleet of robotic systems seamlessly in a way that wasn’t possible until now.
At the heart of the facility lies Sequoia, a state-of-the-art multilevel containerized inventory system that makes it faster and safer for employees to store and pick goods. Sequoia can hold more than 30 million items, which is five times larger than the first deployment of this system in Houston, Texas. This system helps Amazon store products closer to customers for faster deliveries. The system coordinates thousands of mobile robots and a suite of robotic arms to bring items to employees at ergonomic workstations, where they can do all their work with more comfort and safety in their power zone, between mid-thigh and mid-chest.
Once customer orders are picked, a series of new systems helps move these orders through the next-generation site faster so they can be packed for delivery. Packaging Automation optimizes this process while using materials that are curbside recyclable.
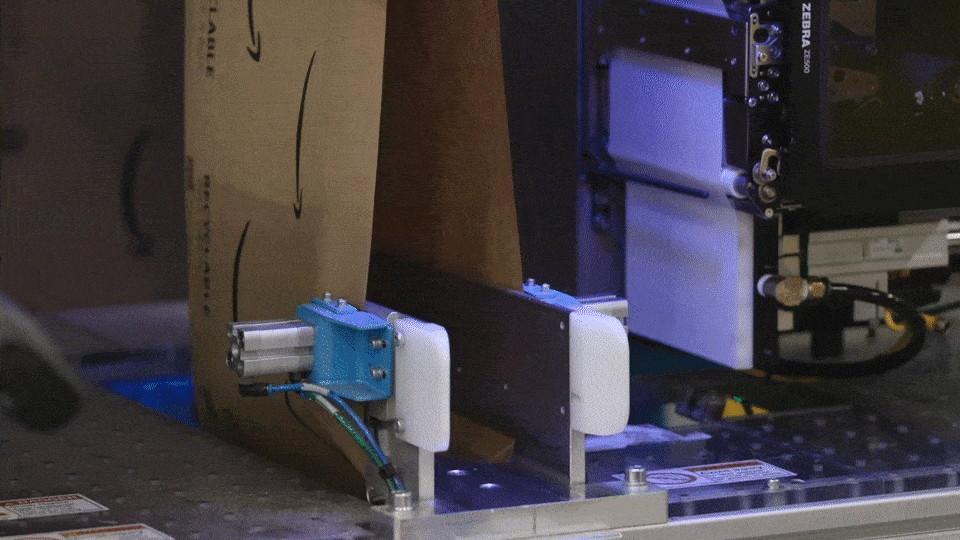
As inventory and packages move through the facility, Robin, Cardinal, and Sparrow—an AI-powered trio of robotic arms—sort, stack, and consolidate millions of items and customer orders with remarkable precision.
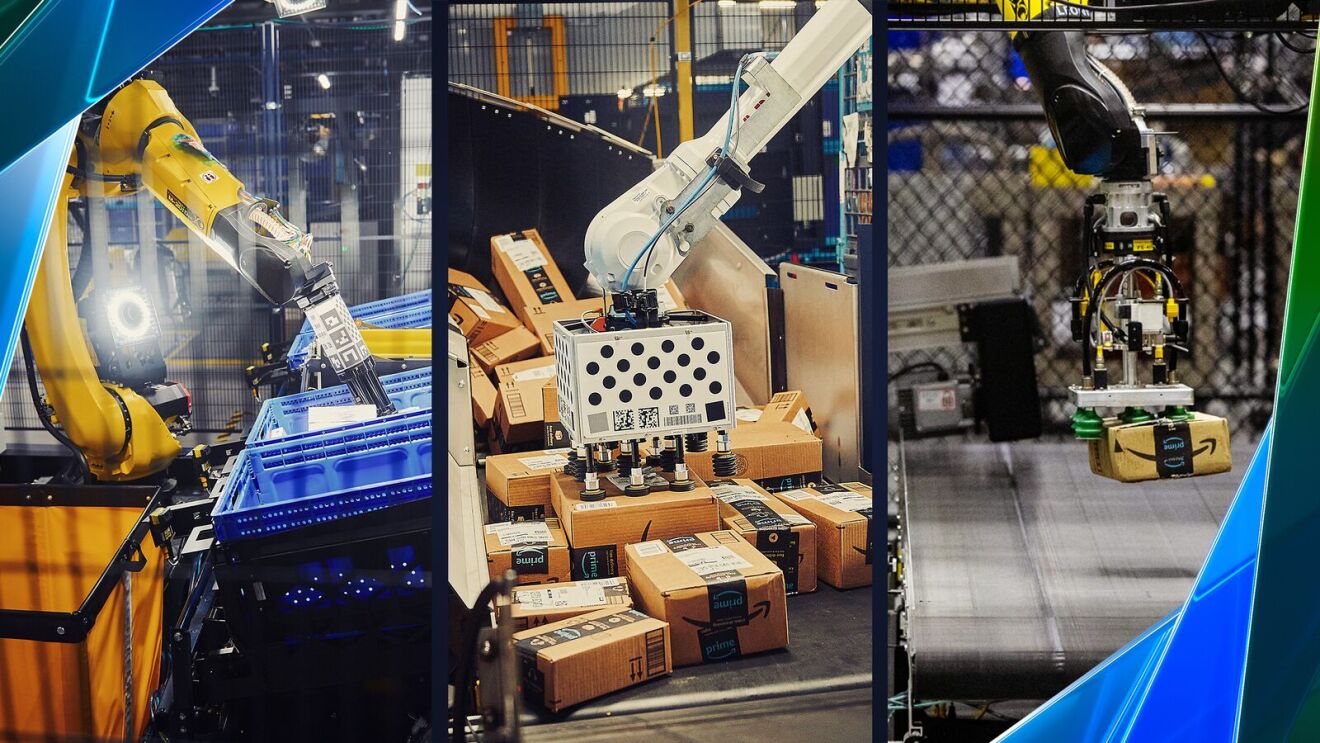
Amazon is continually seeking new ways to reduce packaging and make its materials easier to recycle. Sparrow’s latest version can handle over 200 million unique products of different shapes, sizes, and weights. It uses advanced computer vision and AI systems to be the most versatile and reliable robotic arm in the industry.
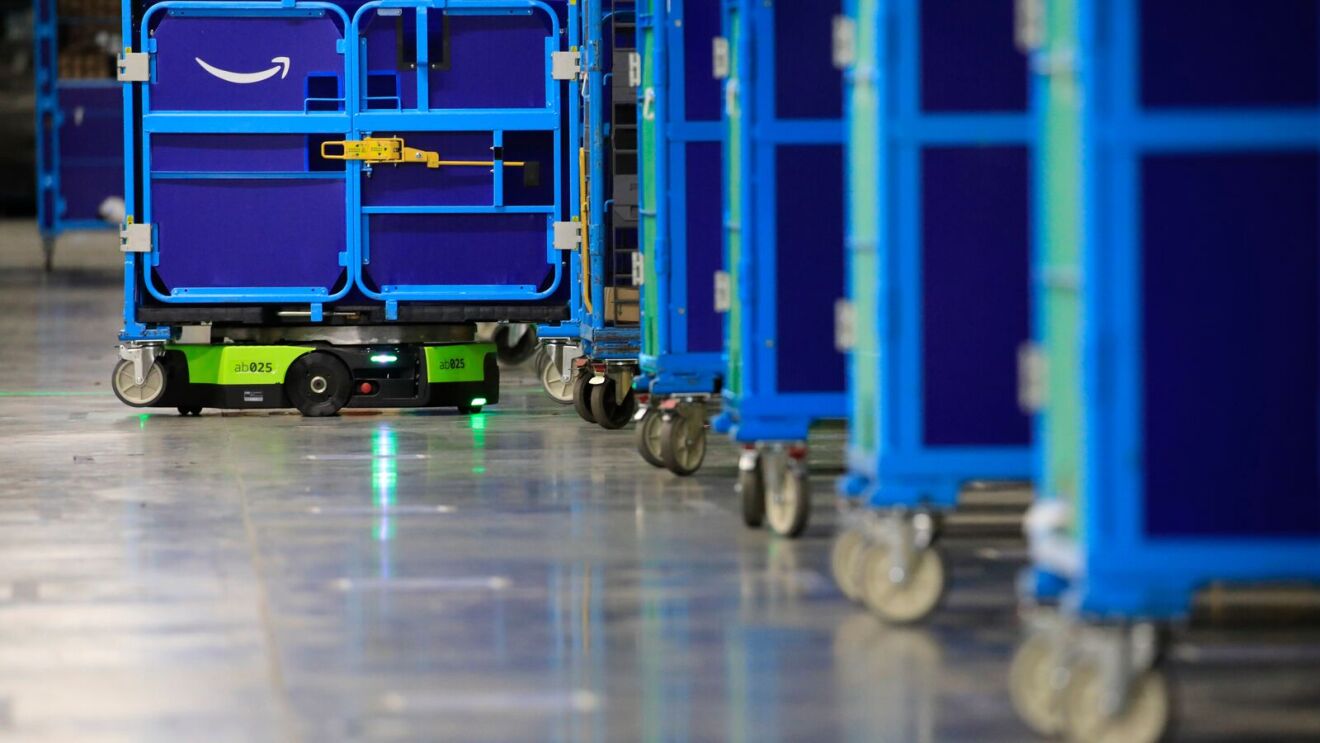
Proteus, Amazon’s first fully autonomous mobile robot, effortlessly navigates carts of packages to the outbound dock so they can be loaded into trucks. Proteus safely moves around employees in open spaces.
These technologies, along with the many thousands of other robotics systems used in Shreveport, bring Amazon’s vision for collaborative technology to life. This vision centers on innovation that supports employees, enhances operational safety and sustainability, and enables Amazon to deliver faster, more efficiently, and more responsibly to customers.
Technology in the next-generation sites unlocks new benefits for employees and customers. Systems like Sequoia, Cardinal, and Proteus will play an important role in supporting Amazon’s company-wide safety objectives. The company expects these sites to build on the 30% improvements in safety they have already achieved over the last several years by improving ergonomics and reducing heavy lifting.
As Amazon deploys this new generation of robotics across its network, the company expects its headcount to continue to grow. This technology is also creating new opportunities for skilled jobs. Next-generation fulfillment centers and those with advanced robotics will require 30% more employees in reliability, maintenance, and engineering roles.
These skilled jobs often require certifications, which Amazon supports through its Career Choice program, offering employees the chance to pursue them at no cost. The company’s mechatronics and robotics apprenticeship provides hourly wages up to 40% higher than entry-level roles, underscoring its commitment to advancing employee careers. According to recent research by MIT, opportunities like these lead employees to embrace new technology and see the benefits they offer as they prepare for the future of work.
Amazon’s commitment to faster delivery for customers remains constant, and the next-generation facilities will play a key role in making this happen. Within these sites, Amazon has reduced fulfillment processing times by up to 25%, improved shipping accuracy, and increased the number of items available for same-day and next-day delivery.
Jane Tschanen, is the director of U.S. employee experience for Amazon fulfillment centers, dedicated to enhancing employee satisfaction and well-being. Amazon’s most advanced fulfillment center is a major step forward, but this milestone is only one chapter in the story of its next wave of robotics and AI innovation. These new robotic systems are engineered for seamless integration across existing buildings as well. This allows the company to modernize its entire network, accelerating the widespread positive impact of this technology and driving efficiency at scale more rapidly than ever before.
During peak delivery seasons, Amazon aims to drive a 25% improvement in its cost to serve at the next-generation facility. These are savings the company can pass on to customers. As AI and robotics reimagine logistics, the scale and impact of this innovation will only grow. The future of Amazon’s work begins now.