Inside Amazon fulfillment centers across North America, a sophisticated artificial intelligence (AI) system is at work. Known as “Project P.I.,” short for “private investigator,” this AI model meticulously scans millions of products daily, from everyday items like dog food and phone cases to apparel like T-shirts and books. The goal is simple: to ensure every customer receives a flawless order, leading to ultimate satisfaction.
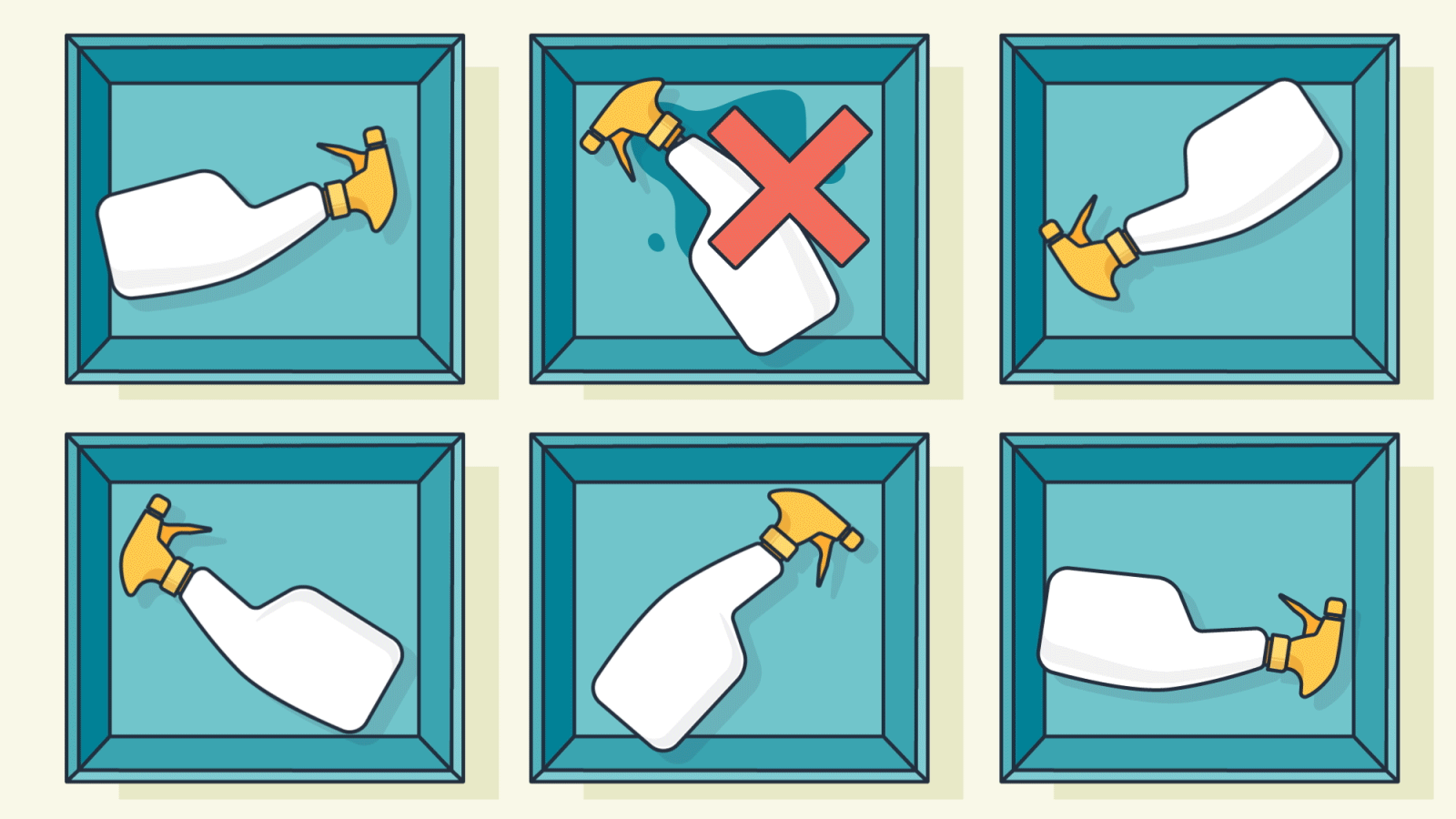
Project P.I. uses a combination of generative AI and computer vision, essentially employing detective-like tools to identify defects. This includes detecting damages – a bent book cover, for instance – or discrepancies in color or size before items ever reach the customer. Beyond simple detection, Project P.I. helps pinpoint the root causes of issues, allowing Amazon to implement preventative measures upstream in the fulfillment process.
In fulfillment centers already using the system, Project P.I. has demonstrated remarkable accuracy in sorting through the massive volumes of items, identifying potential issues with precision.
How Amazon’s ‘Private Investigator’ Works
Before an item is prepared for shipment, it passes through an imaging tunnel. This is where Project P.I. goes to work, employing computer vision to scrutinize the product and assess images for any defects. If a flaw is found, the product is immediately isolated, preventing shipment to a customer. The issue triggers a closer investigation to determine if there is a broader problem with similar items within the inventory.
Amazon associates then review the items flagged by Project P.I. and decide on the product’s fate. Options include reselling the item at a discounted price through Amazon’s Second Chance site, donating it, or finding another suitable use for it. This AI model serves as an extra layer of quality control, complementing the manual inspections performed by associates at several North American fulfillment centers. The technology is set to expand to additional locations throughout 2024.
“We want to get the experience right for customers every time they shop in our store,” said Dharmesh Mehta, vice president of Worldwide Selling Partner Services at Amazon. “By leveraging AI and product imaging within our operations facilities, we are able to efficiently detect potentially damaged products and address more of those issues before they ever reach a customer, which is a win for the customer, our selling partners, and the environment.”
Ensuring a More Sustainable Customer Experience
Project P.I.’s work is more than just a measure to ensure customer satisfaction; it also aligns with Amazon’s commitment to addressing climate change. Using AI innovation helps infuse that commitment into the customer experience.
Preventing the shipping of damaged or defective items results in fewer returns, reducing wasted packaging and unnecessary carbon emissions associated with transportation.
“Amazon is using AI to reach our sustainability commitments with the urgency that climate change demands, while also improving the customer experience,” said Kara Hurst, vice president of Worldwide Sustainability at Amazon. “AI is helping Amazon ensure that we’re not just delighting customers with high-quality items, but we’re extending that customer obsession to our sustainability work by preventing less-than-perfect items from leaving our facilities, and helping us avoid unnecessary carbon emissions due to transportation, packaging, and other steps in the returns process.”
Preventing Future Errors
Amazon teams are using a generative AI system that uses a Multi-Modal LLM (MLLM) to investigate the root cause of negative customer experiences. When a defect is identified through customer feedback, the system uses the information to understand the cause and continuously improve the quality control system. The system first reviews customer feedback and then incorporates images taken from Project P.I. and analyzes other data sources to confirm the issue’s origin.
This technology is also poised to benefit Amazon’s selling partners. If, for example, a selling partner accidentally places incorrect size stickers on a product, Amazon can communicate the error, helping prevent it from repeating in the future. With more than 60% of sales in Amazon’s store coming from independent small and medium-sized businesses, reducing the number of defective products shipped has a ripple effect, decreasing overall returns and increasing customer satisfaction.
Project P.I. demonstrates Amazon’s focus on improving both the customer experience and the experience for selling partners. As AI continues to advance, Amazon will continue to innovate, working towards sustainability goals while exceeding expectations for customers and selling partners.